How Industrial CT Scanning Detects Hidden Defects in Manufacturing
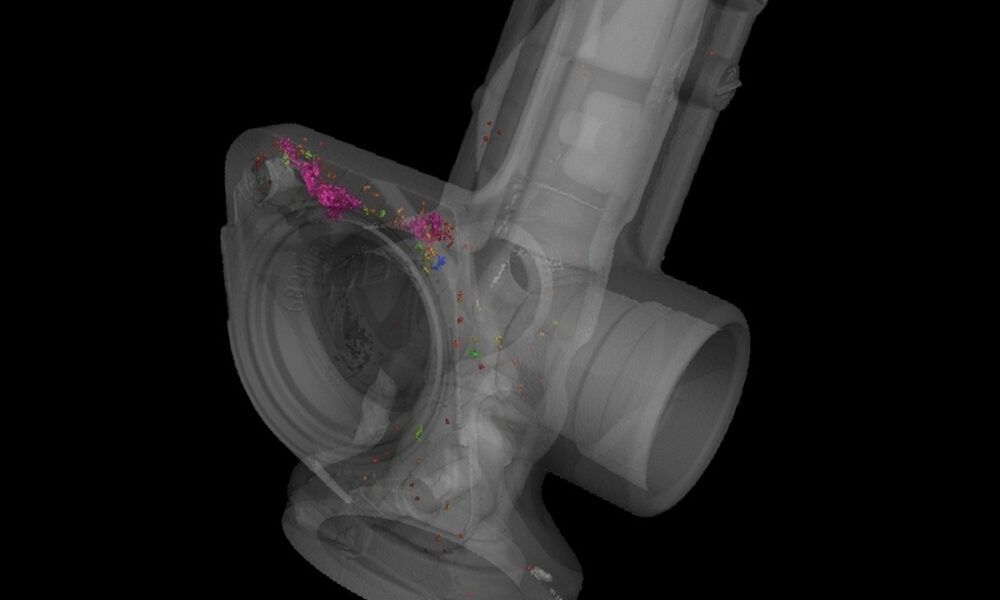
In modern manufacturing, ensuring product quality and reliability is critical. Even minor defects can lead to costly recalls, safety hazards, and reduced customer trust. While traditional inspection methods like visual checks and ultrasonic testing can identify surface-level imperfections, they often fall short in detecting hidden internal flaws. Industrial CT scanning services have emerged as a powerful solution for identifying concealed defects, improving quality control, and optimizing production processes.
What is Industrial CT Scanning?
Industrial CT scanning is a non-destructive testing (NDT) method that utilizes X-ray technology to generate detailed, cross-sectional images of a product. This advanced imaging technique provides a comprehensive internal and external view of components, allowing manufacturers to detect defects that would otherwise go unnoticed.
The process involves:
- X-ray emission: A high-energy X-ray beam passes through the object.
- Detection and image capture: Sensors detect variations in density and structure.
- Reconstruction: Advanced software compiles thousands of 2D images into a precise 3D model.
This technology is widely used across industries, including aerospace, automotive, medical devices, and electronics, where precision and reliability are paramount.
Types of Defects Detected by Industrial CT Scanning
Industrial CT scanning excels at identifying a wide range of defects that could compromise product performance and safety. These include:
1. Porosity and Voids
Tiny air pockets or voids in castings, injection-molded parts, or metal components can weaken structural integrity. CT scanning detects these internal inconsistencies, allowing manufacturers to adjust processes to minimize defects.
2. Cracks and Fractures
Subsurface cracks and fractures, which may not be visible externally, can be pinpointed using CT scans. This is especially useful in industries like aerospace and automotive, where undetected fractures can lead to catastrophic failures.
3. Inclusions and Foreign Material
Unwanted materials, such as contaminants or unintended inclusions in metal or plastic parts, can be detected with high precision. Identifying these defects early prevents product malfunctions and improves reliability.
4. Wall Thickness Variations
Non-uniform wall thickness in molded or machined parts can lead to weak spots and premature wear. CT scanning allows engineers to analyze wall consistency and adjust designs accordingly.
5. Assembly Issues and Misalignment
CT scanning is not only useful for detecting material defects but also for assessing assembly accuracy. It ensures that internal components are properly aligned and fit correctly, reducing failure rates in complex assemblies like medical devices or electronic enclosures.
Benefits of Industrial CT Scanning in Manufacturing
1. Non-Destructive and Highly Accurate
Unlike traditional destructive testing methods that require cutting open a part, CT scanning preserves the component while delivering high-resolution imaging. This allows for thorough inspections without waste.
2. Faster and More Reliable Quality Control
Traditional inspection techniques can be time-consuming and may miss microscopic defects. CT scanning automates the process, significantly reducing inspection time while increasing defect detection rates.
3. Cost Savings and Process Optimization
Early defect detection minimizes the risk of expensive recalls and rework. By identifying process inefficiencies, manufacturers can optimize production methods, reducing material waste and improving overall efficiency.
4. Improved Product Design and Development
CT scanning aids engineers in refining prototypes and final products. By analyzing internal structures and pinpointing weaknesses, manufacturers can enhance designs before mass production, reducing costly design iterations.
5. Regulatory Compliance and Certification
Many industries, especially medical and aerospace, require strict quality assurance. CT scanning provides detailed inspection reports that help companies meet regulatory requirements and achieve necessary certifications.
Industries Benefiting from Industrial CT Scanning
Industrial CT scanning is a game-changer for numerous industries, including:
- Aerospace: Ensuring flawless aircraft components for safety and performance.
- Automotive: Detecting defects in engine components, transmissions, and structural parts.
- Medical Devices: Verifying the integrity of implants, prosthetics, and surgical tools.
- Electronics: Inspecting circuit boards and microchips for hidden defects.
- Additive Manufacturing (3D Printing): Ensuring consistency in printed parts by identifying voids and inconsistencies.
Conclusion
Industrial CT scanning is a revolutionary technology that enhances manufacturing quality by detecting hidden defects with unparalleled accuracy. Its ability to provide non-destructive, detailed internal analysis ensures product reliability, reduces costly errors, and improves overall efficiency. As industries continue to demand higher precision and safety standards, CT scanning remains an indispensable tool for modern manufacturing and quality assurance.